How to Streamline Operations with Regular Packaging Equipment Repair Services
How to Streamline Operations with Regular Packaging Equipment Repair Services
Blog Article
All About Packaging Devices Fixing Providers: Necessary Insights for Keeping Your Equipment
Product packaging tools repair service solutions play an important role in the manufacturing process. They ensure that machinery runs successfully and produce constant results. Regular upkeep and prompt repair work can conserve organizations from expensive downtimes. Nevertheless, numerous operators overlook the indicators that show a requirement for repair. Comprehending these signs and knowing how to choose the right solution provider can greatly impact a firm's efficiency and profits. What should services prioritize to guard their operations?
Understanding the Relevance of Product Packaging Tools Repair
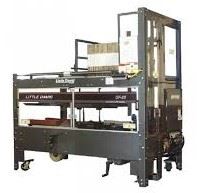
Usual Indications Your Equipment Demands Repair
Determining the indications that product packaging tools requires repair is essential for preserving operational effectiveness. Typical indications include uncommon noises during operation, reduced production effectiveness, and frequent jams or errors. Recognizing these problems early can avoid additional damages and pricey downtime.
Unusual Sounds During Procedure
Unusual noises during procedure can serve as important signs that packaging devices needs repair service. Such noises might consist of grinding, clanking, or piercing whining, which often recommend underlying mechanical problems. Grinding noises may show worn bearings or misaligned parts, while clanking audios might direct to loose parts or foreign things obstructing the machinery. High-pitched yawping might recommend problems with the motor or drive systems. Neglecting these noises can cause more substantial damage and expensive repairs. Normal maintenance checks are important to identify and attend to these acoustic cautions quickly. Operators needs to maintain a keen awareness of their tools's audios, as early discovery of uncommon noises can avoid long term downtime and boost the durability of the machinery.
Reduced Manufacturing Efficiency
Lowered production performance commonly signals that product packaging equipment needs repair service. It can lead to considerable delays and decreased outcome when equipment runs listed below its suitable capacity. This decline may materialize as longer cycle times or a lack of ability to meet production targets. Operators may see a drop in the speed at which products are packaged or filled up, suggesting prospective concerns within the devices. Furthermore, a constant lack of ability to keep established efficiency metrics can further highlight underlying problems. Neglecting these indications can cause greater operational losses and higher expenses. Because of this, timely assessment and repair work of the devices are vital to bring back performance and guarantee that production procedures stay streamlined and reliable. Regular maintenance checks can aid preemptively attend to these concerns.
Constant Jams or Errors
Regularly, product packaging equipment may display indications of malfunction with relentless jams or operational mistakes. These problems can interrupt workflow and result in significant downtime. Typical reasons for constant jams include damaged elements, imbalance, or particles blocking the machinery. Functional errors, on the various other hand, may stem from software program problems, wrong setups, or insufficient maintenance. Acknowledging these indicators early is crucial for protecting against additional damage and making certain consistent manufacturing quality. Normal examinations can help identify potential troubles before they intensify. Dealing with regular jams or mistakes quickly can conserve producers time and money, eventually enhancing general effectiveness. Consequently, prompt repair service solutions are necessary to maintain peak performance and expand the lifespan of product packaging equipment.
Preventative Upkeep Strategies
Preventative maintenance methods are vital for ensuring the long life and performance of packaging equipment. Implementing arranged maintenance periods, carrying out regular inspections, and utilizing correct lubrication and cleaning techniques can considerably lower the probability of unexpected failures. These practices not only boost devices performance but also optimize functional productivity.
Scheduled Upkeep Intervals
Arranged upkeep periods play an important function in guaranteeing the durability and efficiency of product packaging devices. By establishing a normal maintenance timetable, business can proactively resolve prospective issues prior to they escalate right into expensive repair services or downtime. These intervals ought to be tailored to the specific equipment and its functional demands, thinking about variables such as usage regularity and environmental problems. Implementing a structured approach to scheduled maintenance makes it possible for operators to maximize performance and lower the threat of unforeseen failings. Furthermore, sticking to these intervals can boost safety criteria and enhance total performance. Inevitably, well-planned upkeep schedules are important in maintaining the capability of packaging equipment and prolonging its functional life expectancy, ensuring a trusted manufacturing process.
Routine Evaluation Practices
While tools may seem operating well, regular inspection methods are necessary for recognizing prospective concerns before they impact production. These inspections must consist of a complete exam of critical components, such as sensing units, equipments, and belts, to assure they run within defined specifications. Regularly looking for indications of wear, misalignment, or uncommon noises can help identify troubles early. In addition, documenting inspection searchings for can create a valuable background that aids in future troubleshooting. Operators ought to be trained to identify typical indicators of malfunction, facilitating timely intervention. Utilizing an organized method to routine inspections not only boosts equipment dependability however likewise reduces unintended downtime, inevitably boosting total operational efficiency and efficiency.
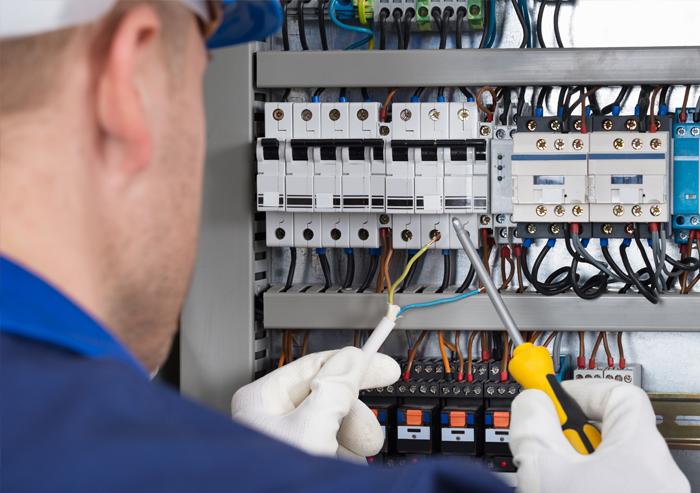
Lubrication and Cleaning Up Techniques
Routine inspections prepared for effective upkeep, yet lubrication and cleansing techniques play a necessary role in maintaining devices efficiency. Correct lubrication minimizes friction between moving components, minimizing deterioration while enhancing the efficiency of equipment. It is vital to use the ideal kind and quantity of lube, as defined by the tools maker. Regular cleaning gets rid of dirt, debris, and contaminants that can impede capability, ensuring suitable operation. Methods such as utilizing soft brushes, compressed air, or vacuum cleaner systems can efficiently maintain sanitation without harming sensitive parts. Packaging Equipment Repair Services. Establishing a regular timetable for both lubrication and cleaning not just prolongs the equipment's link lifespan but also greatly reduces the chance of unanticipated breakdowns, inevitably leading to enhanced performance in product packaging procedures
Picking the Right Repair Solution copyright
Just how can a business warranty it selects one of the most appropriate product packaging tools fixing company? To make an educated option, companies ought to initially evaluate the service provider's experience and credibility in the industry. This can be achieved through online evaluations, testimonials, and suggestions from other businesses.Next, evaluating the service provider's credentials and certifications is crucial, as these suggest a dedication to industry requirements and ideal practices. Furthermore, businesses ought to ask about the variety of solutions supplied, ensuring that the provider can resolve certain machinery issues.Cost is also a considerable element; obtaining comprehensive quotes and understanding the rates structure will aid stay clear of unexpected expenditures. Prompt action and accessibility for emergency repairs can considerably influence the choice, as tools downtime can lead to significant losses. By meticulously considering these aspects, businesses can select a packaging devices fixing provider that straightens with their operational requirements.
The Repair work Process: What to Expect
Expense Considerations for Packaging Devices Repairs
While the expense of product packaging tools repairs can differ significantly based upon several elements, comprehending these variables can help companies spending plan effectively. Trick aspects affecting repair work costs consist of the sort of equipment, the extent of the damages, and the availability of substitute parts. For example, specialized or older tools might need extra costly components, driving up expenses. Labor prices additionally play a considerable duty; service technicians with specialized knowledge may bill greater costs. Furthermore, the necessity of the repair can affect rates, as expedited services normally sustain additional costs. Companies should additionally consider the possible downtime related to repair work, which can cause lost earnings. By assessing these variables, companies can develop a more accurate monetary strategy for repair and maintenance, ensuring they designate adequate sources while lessening unexpected costs. Recognizing the total expense of possession is essential for effective budgeting and long-lasting operational efficiency.
Tips for Expanding the Life-span of Your Equipment
To make best use of the life-span of product packaging equipment, services must execute a proactive maintenance technique that consists of routine inspections and timely maintenance. Set up exams can assist determine minor concerns before they intensify, preventing pricey repairs and downtime. Correct training for operators is likewise crucial; experienced personnel can acknowledge very early indicators of wear and promptly address them.Additionally, keeping equipment complimentary and tidy from particles guarantees peak performance and decreases wear on elements. Using high-grade lubricants and complying with manufacturer guidelines for parts replacement can better enhance long life. Companies need to also keep a precise log of maintenance activities, which assists in tracking efficiency fads and organizing future services.Finally, purchasing top quality substitute parts instead of choosing cheaper options can significantly affect equipment toughness. By complying with these ideas, business can promote a more dependable and efficient production environment, eventually prolonging the life-span of their product packaging tools.
Often Asked Inquiries
How Usually Should I Set Up Repair Work for My Devices?
The frequency of arranged repairs for tools depends on usage, maker recommendations, and maintenance background. Proactive approaches and normal assessments can help figure out suitable intervals, ensuring efficiency and decreasing unforeseen breakdowns for durability.
Can I Perform Fixes Myself, or Should I Employ an Expert?
The specific contemplated whether to undertake repair services individually or involve an expert. While some minor fixes may be convenient, intricate concerns commonly require specialized abilities and devices, making professional assistance the more secure and extra efficient alternative.
What Warranties Are Readily Available for Repair Work Services?
Different warranties for repair service visit this page solutions exist, frequently covering components and labor for particular periods. Clients should inquire concerning service warranties, as reputable service providers typically provide warranties to ensure high quality and consumer complete satisfaction in their repair work.
Exactly how Do I Pick the Right Components for My Machinery?
Choosing the right parts for equipment entails reviewing compatibility, quality criteria, and producer specs. Looking into trusted distributors and consulting with professionals can likewise ensure peak efficiency and longevity of the equipment in inquiry.
What Certifications Should a Fixing Professional Have?
When thinking about qualifications for a repair work specialist, one ought to focus on industry-standard qualifications, such as those from the National Institute for Qualification in Engineering Technologies, in addition to specific manufacturer training to guarantee proficiency in relevant equipment. Product packaging tools repair solutions Read More Here play a crucial function in the manufacturing procedure. Numerous firms focus on purchasing new product packaging tools, understanding the importance of repair work services is necessary for keeping operational efficiency (Packaging Equipment Repair Services). Recognizing the signs that product packaging tools requires repair service is necessary for preserving functional efficiency. Reduced manufacturing performance frequently indicates that product packaging tools requires repair work. Exactly how can a business warranty it chooses the most ideal packaging devices repair work solution copyright?
Report this page